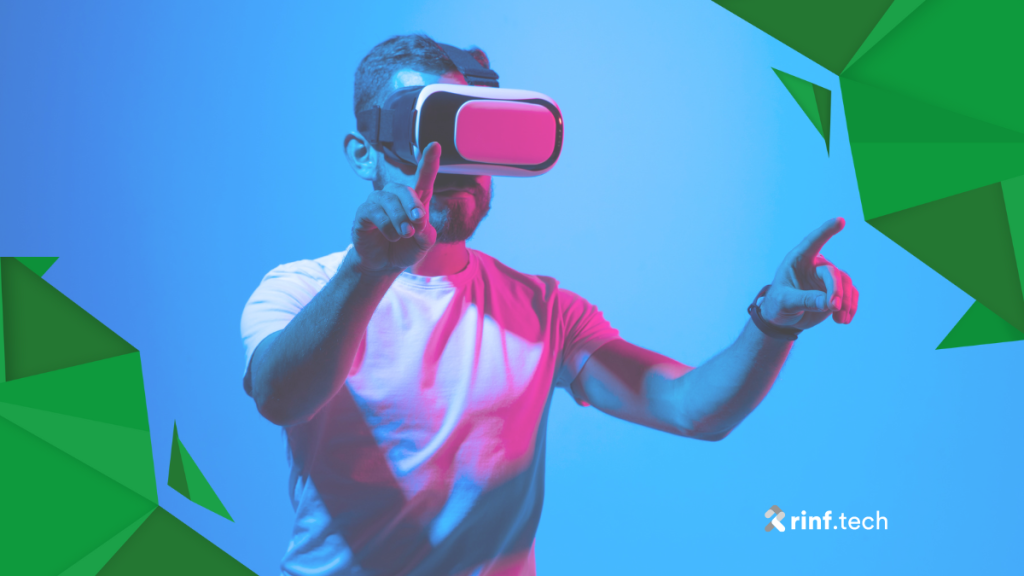
Mixed Reality Use Cases and Challenges in 2024
The article dives deep into the world of Mixed Reality, its use cases across industries, trends, challenges, and the future outlook.
In recent years, the global industrial automation market has seen significant growth, projected to reach $218.8 billion by 2027. This growth is fueled by technological advancements such as AI, IoT, and robotics, revolutionizing manufacturing processes and enabling more complex and efficient production systems.
Amidst these technological advancements, Augmented Reality (AR) stands out as a game-changer, ready to redefine the boundaries of industrial automation. AR technology, with its ability to overlay digital information onto the real world, creates a unique blend of physical and digital environments. This integration not only enhances operational efficiency and reduces errors but also provides workers with intuitive and interactive tools, thereby improving productivity and safety.
According to recent statistics, the AR market is expected to grow from $93.67 billion in 2024 to $1,869.40 billion by 2032, This rapid growth highlights AR’s transformative potential across multiple industries, including manufacturing.
This article delves into AR’s impact on industrial automation. From training and maintenance to collaborative problem-solving and inventory management, AR is set to revolutionize how industries operate, aligning with the broader goals of Industry 4.0 to create a more connected, smart, and efficient manufacturing ecosystem.
AR revolutionizes industrial automation by overlaying digital information in the real world, creating a more interactive and intuitive work environment. This technology bridges the gap between physical machinery and digital data, enhancing the efficiency and accuracy of industrial operations. AR provides real-time data visualization, enabling workers to access important information without interrupting their workflow. This capability is particularly transformative in manufacturing, where downtime and errors can be costly.
According to PwC, VR and AR are expected to contribute approximately $1.8 trillion$1.8 trillion (about $5,500 per person in the US) to global GDP by 2030, with AR accounting for around $1.3 trillion (about $4,000 per person in the US) of that total, highlighting the significant economic impact of these technologies.
The core functionalities of AR include real-time data overlay, 3D visualization, and interactive guidance. These features are more than just tools; they can empower workers. AR allows workers to visualize complex data sets, such as equipment schematics and operational metrics, directly on their working machinery. This real-time interaction reduces the cognitive load on workers and enhances their ability to perform tasks accurately and efficiently. Moreover, AR’s ability to provide contextual information hands-free is particularly beneficial in environments where safety and precision are vital.
In addition to enhancing operational efficiency, AR fosters a more immersive and engaging work environment. By providing interactive and intuitive tools, AR empowers workers to perform tasks with greater confidence and precision. This technology also facilitates remote assistance and collaboration, allowing experts to guide on-site technicians through complex procedures in real-time.
AR Application in Industrial Automation
Augmented Reality is making significant progress in industrial automation, offering innovative solutions that enhance training, streamline maintenance, facilitate remote collaboration, and optimize inventory management. From reducing training times to improving maintenance accuracy, AR is set to redefine the industrial landscape, making operations more connected and intelligent.
AR is transforming training and skill development in industrial settings by providing immersive and interactive learning experiences. AR overlays enable workers to see step-by-step instructions and 3D visualizations directly on the equipment they are training to use. This method significantly reduces training time and enhances knowledge retention. For example, a study by the National Training Laboratories found that learning retention rates could reach 75% with AR/VR training compared to traditional methods, which typically achieve only a 10-20% retention rate.
Companies like Boeing have implemented AR in their training programs, resulting in a 30% reduction in assembly time and a 90% improvement in first-time quality. This demonstrates the substantial impact AR can have on workforce efficiency and competency.
AR enhances maintenance and repair operations (MRO) by directly overlaying real-time data, schematics, and repair procedures onto machinery. This capability allows technicians to access crucial information quickly, reducing the need to consult user manuals and minimizing errors.
According to recent statistics, AR for maintenance and repair helps speed up MRO activities by 15–30% and improve work quality by 90%, significantly reducing MRO costs.
Furthermore, a report by Deloitte highlights that AR can significantly improve first-time fix rates, reducing downtime and associated costs by providing technicians with instant access to expert knowledge and detailed instructions. This streamlined approach is particularly beneficial in industries with critical equipment uptime, such as manufacturing and utilities.
AR facilitates real-time collaboration and remote assistance by allowing experts to see what on-site technicians see through smart glasses or mobile devices. This capability enables remote experts to provide immediate guidance and troubleshooting assistance, reducing downtime and travel costs.
For instance, our robot arm digital twin PoC, driven by MS HoloLens, showcases how AR can enable real-time, remote manipulation and monitoring of robotic arms. It improves operations efficiency, safety, and precision, allowing for seamless interaction and control of robotic systems in manufacturing, assembly, and maintenance tasks. Operators can anticipate and correct potential issues by providing a virtual representation that mirrors the physical robot, optimizing workflow and reducing downtime.
According to a survey by Capgemini, 82% of companies currently implementing AR/VR report that the benefits are either meeting or exceeding their expectations. This real-time knowledge sharing is precious in complex industrial environments where specialist expertise is often required.
AR transforms inventory management and warehouse operations by providing workers with real-time data overlays that display stock levels and optimal picking routes directly in their field of view. This technology enhances efficiency and accuracy, minimizing search times and optimizing warehouse layouts. Companies like DHL have successfully implemented AR in their warehouses, resulting in a 25% increase in productivity and significantly reduced training times for new staff. These improvements emphasize the potential of AR to streamline logistics and inventory management processes.
The adoption of AR is closely aligned with the goals of Industry 4.0, which aims to foster a more connected, intelligent, and efficient manufacturing ecosystem. Industry 4.0, characterized by integrating cyber-physical systems, IoT, and cloud computing, seeks to create smart factories where machines and humans interact seamlessly. AR plays a crucial role in this transformation by providing real-time insights, enhancing human-machine interfaces, and enabling data-driven decision-making.
AR’s role in Industry 4.0 is not just about transformation but also about enhancing productivity and efficiency. By overlaying digital information onto physical equipment, AR empowers workers to perform tasks more accurately and quickly. Siemens, for instance, has integrated AR into its production processes, resulting in a 34% reduction in the time required for specific assembly procedures and a significant decrease in error rates. This is a promising sign for the future of manufacturing.
AR’s contribution to Industry 4.0 goes beyond productivity and efficiency. It also significantly improves process optimization. By providing real-time data visualization and interactive simulations, AR allows for better monitoring and control of manufacturing processes. Boeing‘s use of AR in wire harness assembly for aircraft is a testament to this. The implementation of AR has led to a 25% reduction in production time and a 40% increase in productivity, demonstrating the significant potential of AR in optimizing intricate and labor-intensive processes.
Furthermore, AR facilitates enhanced data-driven decision-making, a pillar of Industry 4.0. By integrating AR with IoT sensors and big data analytics, companies can gain real-time insights into machine performance and operational efficiency.
In addition to operational benefits, AR supports the broader goals of Industry 4.0 by promoting sustainability and resource efficiency. By optimizing maintenance schedules and reducing errors, AR helps minimize waste and extend the lifespan of machinery.
The implementation of AR also enhances workforce collaboration and knowledge sharing. In smart factories, AR enables remote experts to provide real-time guidance and support to on-site workers, regardless of geographic location. This capability reduces travel costs and ensures that critical issues are addressed promptly, enhancing overall operational resilience.
As AR technology continues to evolve and integrate with other Industry 4.0 technologies, its role in shaping the future of industrial automation will only expand, paving the way for smarter, more efficient, and sustainable industrial operations.
While Augmented Reality presents immense potential for transforming industrial automation, several challenges must be addressed to ensure its successful and widespread adoption. Overcoming them will require strategic planning, innovation, and continuous advancements in AR technology.
One of the primary barriers to AR adoption in industrial automation is the significant initial investment required for hardware, software, and implementation. AR devices like Microsoft HoloLens or Magic Leap are relatively expensive, and developing custom AR applications tailored to specific industrial needs can further add to the costs. Smaller companies may find these costs overwhelming. To address this, some companies are exploring leasing options and phased rollouts to spread the financial burden over time.
Integrating AR with existing industrial systems and workflows can be complex and time-consuming. Industrial environments often consist of legacy equipment and diverse software systems that may need to be more readily compatible with new AR technologies. Successful integration requires a thorough understanding of the existing infrastructure and the capabilities of AR solutions. Companies like Caterpillar have approached this challenge by developing customized AR solutions to interface with their existing equipment and data systems. This demonstrates that tailored integration is possible but requires substantial effort and expertise.
For AR to be effective, it must be embraced by the workforce. This requires not only technical training but also overcoming resistance to change. Employees may hesitate to adopt new technologies due to concerns about job security, usability, and the learning curve associated with AR devices. A survey by Deloitte revealed that more workers worldwide expressed concerns about adapting to new technologies, including AR. Comprehensive training programs and user-friendly AR interfaces are essential to mitigate these concerns. For example, Lockheed Martin implemented a successful AR training program that reduced the training time for complex assembly tasks by 85%, highlighting the importance of effective training in promoting adoption.
As AR systems become more integrated with industrial networks, they also become potential targets for cyberattacks. The increased connectivity that AR provides can create vulnerabilities if not properly secured. According to a report by Cybersecurity Ventures, the global cost of cybercrime is expected to reach $10.5 trillion annually by 2025. Ensuring robust cybersecurity measures is crucial to protecting sensitive industrial data and maintaining operational integrity. More companies invest heavily in cybersecurity solutions to safeguard their AR applications, emphasizing the importance of secure AR implementation in industrial environments.
Despite these challenges, continuous advancements in AR technology are making it more accessible and affordable. AR hardware costs are gradually decreasing as the technology matures and economies of scale are realized. Additionally, developing more versatile and user-friendly AR software platforms simplifies the integration process. According to IDC, European augmented reality and virtual reality spending is projected to reach $4.8 billion in 2024, indicating a strong trend toward broader adoption. This growth is driven by the increasing recognition of AR’s benefits in enhancing productivity, efficiency, and safety in industrial settings.
To overcome these challenges, companies must adopt a strategic approach that includes thorough planning, pilot testing, and phased implementation. Collaboration with AR solution providers can help customize applications for industrial needs. Investing in employee training and creating a culture that embraces technological innovation is crucial for successful AR adoption. Companies that proactively address these challenges and leverage the continuous advancements in AR technology will be well-positioned to unlock the full potential of AR in industrial automation.
Augmented Rreality holds groundbreaking potential in propelling industrial automation to new heights, particularly in safety. By seamlessly blending digital information with the physical world, AR enhances operational efficiency, accuracy, and, most importantly, safety across various industrial processes. The technology’s ability to provide real-time data visualization, interactive guidance, and immersive training experiences is revolutionizing industries’ operations.
To fully harness AR’s transformative power, companies must take the lead in embracing and integrating this technology into their operations. Partnering with an expert technology provider like rinf.tech can provide the necessary expertise and support to navigate the complexities of AR implementation. By investing in AR, companies can stay ahead of the curve, improve their competitive edge, and achieve new levels of operational excellence.
Augmented Reality is set to redefine the landscape of industrial automation and companies will be at the forefront of this transformation. AR offers unique opportunities for efficiency, innovation, and growth.
Let’s talk.
The article dives deep into the world of Mixed Reality, its use cases across industries, trends, challenges, and the future outlook.
This article explores why and when businesses should consider building custom digital twins and what to take into account before jumping on the digital twin development project.
This article focuses on the key technological changes enterprises need to make in order to support their innovation goals and how R&D can be an effective solution and a driver of IIoT success and sustainability.
Copyright © 2023 rinf.tech. All Rights Reserved.
Terms & Conditions. Cookie Policy. Privacy Policy.
Politica Avertizari de Integritate (RO)