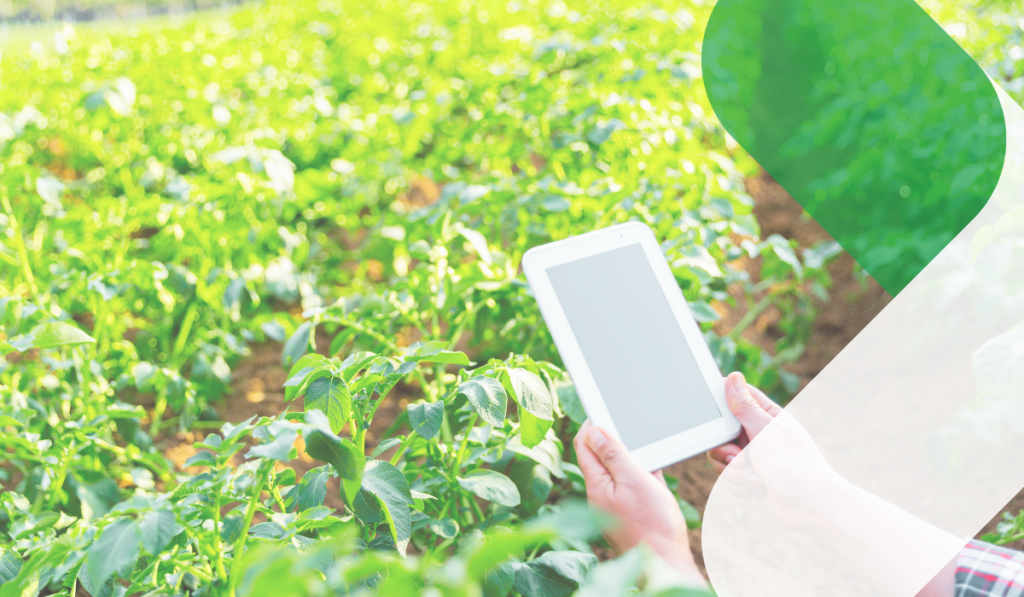
How IoT is Revolutionizing Agriculture: Key Innovations and Future Prospects
Discover how IoT is transforming traditional farming through key innovations, real-world success stories, and future trends that are shaping the agricultural sector.
In this article, we’ll look at the benefits of creating customized digital twins and how digital twin technology can help enterprises prepare for the future and be more resilient to tech challenges.
According to Precedence Research, in 2022, the global digital twin market size was recorded at $11.55 billion, and it is expected to reach approximately $159.77 billion by 2030, with a CAGR of 38.87% during the forecasted period from 2022 to 2030.
The COVID-19 pandemic had a mixed impact on the digital twin market. While the widespread outbreak of the virus increased the adoption of digital twinning in various industries such as workflow, automotive, transport, and aerospace, the shutdown of nations and reduced development and utilization of digital technologies hampered market growth. However, post-pandemic, the increased utilization of digital twin technology is expected to propel the market during the forecast period.
The market drivers for digital twinning include:
The use of digital twin technology enables augmentation of performance and modification of physical prototypes, driving market growth through new developments.
Additionally, the application of digital twin technology in various industries has expanded production and manufacturing, increased internet connections, and better management of assets and processes, resulting in improved productivity and reduced time without human interference. These factors contribute to the market growth rate of digital twinning.
The concept of digital twinning involves creating a digital replica of a real-world process or system, which includes various activities such as stimulation, integration, testing, monitoring, and maintenance. By synchronizing real-time processes with their digital counterparts, digital twinning enhances the connectivity between physical and digital systems. This technology is based on the Internet of Things (IoT) and involves the installation of sensors on physical products to collect data and improve communication.
Initially, NASA pioneered the concept of digital twin technology by creating life-size replicas of early space capsules. These mockups were utilized on the ground to replicate and diagnose issues occurring in orbit. As time passed, fully digital simulations replaced physical replicas as the primary method for space exploration.
The initial phase of creating a digital twin is carried out by specialists, frequently with data science or applied mathematics knowledge. These programmers investigate the fundamental physics of the physical system or object being replicated. They use the information they gather to build a mathematical model that can simulate the original object in virtual space.
The digital twin is designed to receive input from sensors that gather data from the corresponding real-world object. This enables the twin to replicate the physical object in real-time and provide valuable insights into its performance and any potential issues. Additionally, the twin could be developed based on a prototype of the physical object, which can offer feedback as the product is refined. Sometimes, the digital twin can even act as a prototype before any physical version is constructed.
The digital twin technology allows objects such as offshore oil platforms, aircraft engines, trains, and turbines to be virtually designed and tested before being physically produced. Furthermore, digital twins can also assist in maintenance operations by enabling technicians to test proposed equipment fixes before implementing them.
Digital twin technology has numerous business applications in various sectors.
There are three main opportunities in the market for digital twin technology.
Businesses can benefit from creating custom digital twins that may not be possible with off-the-shelf options. A more accurate representation of a company’s assets and processes is made possible by the tailored strategy provided by custom digital twins. Custom digital twins, as opposed to generic solutions, can be created to precisely match the specifications and needs of the company, giving a more thorough representation of their operations. Businesses can build digital twins that specifically reflect their operations using this customized strategy and can use these twins to pinpoint areas for optimization and improvement.
Custom digital twins can be created to solve specific business problems. For instance, a company could enhance quality control, reduce energy use, or optimize production methods. With real-time insights into asset performance and behavior, custom digital twins can be designed to concentrate on these areas for development, allowing businesses to make better decisions about upkeep, repairs, and upgrades. Business operations can be made more productive, downtime can be minimized, and total performance can be improved by utilizing the insights offered by digital twins.
By developing custom digital twins, businesses can address their unique requirements and challenges with a customized strategy. Companies can pinpoint areas for optimization and development by giving a more accurate representation of their assets and processes. Additionally, since they offer real-time insights into asset performance and behavior, customized digital twins can be created to concentrate on areas that need development. This allows companies to make better operational decisions. Businesses can optimize operations, cut costs, and remain ahead of the competition with the help of custom digital twins.
Building and managing digital twins is complex, so specialized companies typically undertake this as part of their R&D and custom product development services. These companies oversee the entire lifecycle of the digital twin, providing custom onboard data collection platforms, applications, dashboards, and tools that leverage the capabilities of digital twin technology.
Building and managing digital twins is complex, so specialized companies typically undertake this as part of their R&D and custom product development services. These companies oversee the entire lifecycle of the digital twin, providing custom onboard data collection platforms, applications, dashboards, and tools that leverage the capabilities of digital twin technology.
It’s likely that your organization recognizes the importance of data and digitization but may need more expertise and resources to capitalize on it entirely. To address this, consider outsourcing digital twin development and data processing and analytics to a technology solutions company, freeing up your time to focus on applying the insights they generate. A grasp of the digital twin life cycle can aid in identifying the specific capabilities required from a custom digital twin software development company.
During the development phase, a toolkit is constructed for the purpose of generating distinct digital twins for a wide range of assets. This stage is considered the most challenging aspect of the digital twin life cycle and typically requires the expertise of specialized data scientists, machine learning specialists, and other professionals working in R&D. This process entails collecting information on the physical attributes of the asset, its operational context, and any associated conditions. Additionally, data automatically collected from the asset establishes machine learning techniques. The output of this phase is a mathematical model that can simulate the behavior and performance of the asset.
Building successful digital twins requires selecting the right technological partner. Creating digital twins can be a challenging process that requires a high level of technological expertise in data analytics, cloud computing, and machine learning.
To create custom digital twins that satisfy their unique wants and requirements, businesses must collaborate with an experienced software development company.
Rinf.tech has firsthand experience building AR-based digital twins. We have a team of specialists who have a thorough grasp of data analytics, machine learning, and digital twin technology. They ensure that the digital twin solution is optimized for efficiency, security, and scalability by using cutting-edge technologies and tools to precisely create digital twins that represent a company’s distinct operations.
Choosing Rinf.tech for your digital twin development offers a range of benefits. The company has a dedicated R&D Embedded Business Unit specializing in custom software product engineering and proof-of-concept (PoC) project development. With expertise in machine learning, deep learning, virtualization, cloud, IoT devices and protocols, wireless modules, and more, Rinf.tech can deliver highly sophisticated and customized digital twin solutions.
From computer vision-powered intruder detection software to robotic arms and their digital twins to sophisticated deep learning models, we at Rinf.tech offers cutting-edge solutions to help businesses thrive in the digital age.
Digital twins offer numerous benefits, enhancing the performance of both processes and products, often resulting in increased operational efficiency. By enabling us to anticipate potential issues in advance, digital twins reduce product defects and shorten production times. They also optimize production processes through real-time information, reducing unplanned downtime due to possible errors and the number of accidents. Additionally, digital twin technology helps to lower maintenance costs by facilitating preventive maintenance tasks and offering opportunities for continual improvement through simulations and identifying failures and inefficiencies.
As a valuable Industry 4.0 tool, digital twins should be leveraged to ensure your organization is well-equipped for the future.
At Rinf.tech, we have a full-fledged R&D Embedded Business Unit that specialises in custom software product engineering and proof-of-concept (PoC) project development. From computer vision powered intruder detection software to robotic arm and its digital twin to sophisticated deep learning models, we use experimental approaches and lessons learned to build top-notch solutions and prototypes to future-proof business ideas and emerging tech.
Discover how IoT is transforming traditional farming through key innovations, real-world success stories, and future trends that are shaping the agricultural sector.
Delving into the IoT device onboarding requirements, challenges and implementation best practices across smart home, industrial, and healthcare settings.
Delving into the complexities of AIoT, exploring its core principles, current state, challenges, and future trends.
Copyright © 2023 rinf.tech. All Rights Reserved.
Terms & Conditions. Cookie Policy. Privacy Policy.
Politica Avertizari de Integritate (RO)