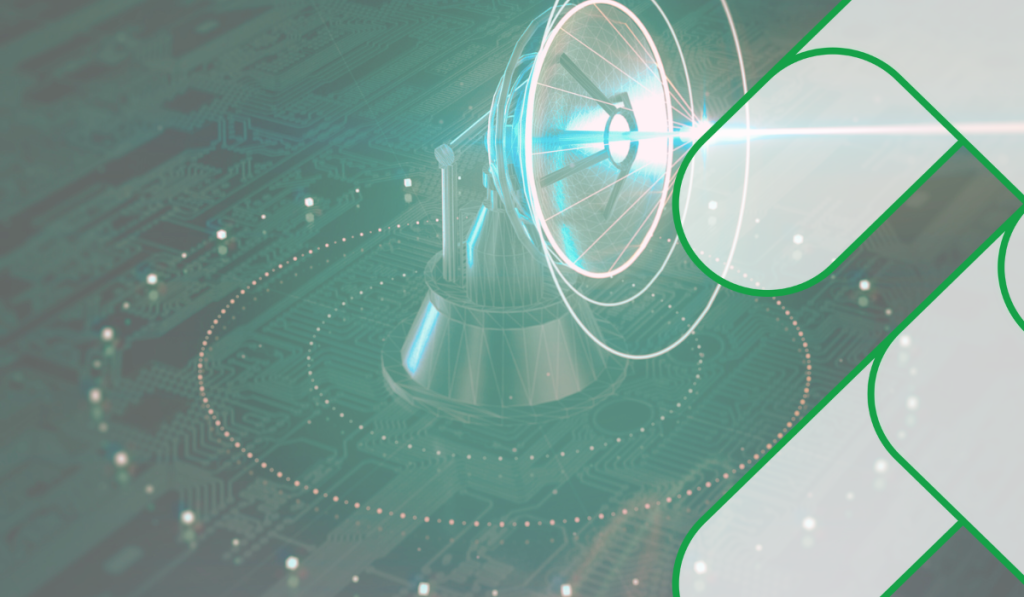
AI-Powered LiDAR: A New Era of Perception
How AI and ML enhance LiDAR technology by overcoming data processing challenges, enabling advanced applications in autonomous systems, robotics, and 3D mapping, and more.
According to the International Energy Agency, electric vehicle sales exceeded 14 million units in 2023, marking a 112% increase compared to 2021. Additionally, automotive manufacturers are under scrutiny to align their operations with global climate targets, including the European Union’s goal of reducing greenhouse gas emissions by 55% by 2030. This evolving landscape has prompted a reimagining of traditional processes, with companies adopting innovative approaches to materials, production, and end-of-life vehicle management.
This article explores the importance of these advancements, showcasing the environmental and economic benefits of integrating sustainable materials, modern manufacturing techniques, and robust recycling practices into the automotive value chain. By embracing sustainability, the industry mitigates its impact on the planet while unlocking new opportunities for growth and innovation in a rapidly changing market.
Bio-based plastics and polymers represent a promising alternative to traditional petroleum-based materials, leveraging renewable resources like corn, sugarcane, and algae. These materials are increasingly being adopted in automotive manufacturing, with applications spanning vehicle interiors, exteriors, and various components. For example, manufacturers use bio-based polymers in seat cushions, door panels, and engine covers, showcasing their versatility. Beyond reducing dependence on fossil fuels, bio-based plastics offer environmental benefits such as lower carbon emissions. While some are biodegradable, others—like bio-polyethylene—provide renewable alternatives without necessarily breaking down biologically.
However, challenges persist, particularly in achieving the necessary durability and performance standards for demanding automotive applications. Additionally, scaling production to meet industry needs while maintaining cost competitiveness remains a hurdle. Despite these challenges, ongoing R&D positions bio-based plastics as a cornerstone of sustainable automotive design.
Recycled materials are becoming integral to sustainable automotive manufacturing, as they help reduce waste, conserve natural resources, and lower production costs. The use of recycled metals, plastics, and textiles is expanding rapidly, with automakers increasingly embracing closed-loop recycling systems. These systems ensure that materials recovered from end-of-life vehicles are processed and reused to produce new cars.
For instance, the German automaker Audi is embracing sustainable materials as a crucial step toward achieving its goal of becoming net CO2 neutral by 2050. In an innovative initiative, Audi uses polyester yarn derived from recycled PET bottles, making up 89% of the upholstery in its fourth-generation A3 model.
Using lightweight materials is critical to improving fuel efficiency and extending the range of electric vehicles (EVs). High-strength steel, aluminum alloys, carbon fiber, and magnesium are increasingly integrated into vehicle design to reduce overall weight without compromising safety or performance. For instance, carbon fiber is used in high-performance vehicles to achieve exceptional strength-to-weight ratios, while aluminum alloys are becoming standard in body panels and chassis components. These materials enhance energy efficiency, improve handling, and reduce wear on components.
Despite their benefits, the adoption of lightweight materials is not without challenges. Significant barriers remain to high production costs, energy-intensive manufacturing processes, and limited recycling infrastructure for advanced composites like carbon fiber. Emerging recycling methods, such as pyrolysis, are helping recover fibers andreduce environmental impact, signaling progress in addressing these challenges. Nevertheless, advancements in material science and production technology are gradually making lightweight materials more accessible for mass-market vehicles.
Nickel has emerged as a critical material in the automotive sector, particularly in producing high-performance batteries for electric vehicles. As a crucial component in lithium-ion batteries, nickel significantly enhances energy density and extends battery lifespan, making EVs more efficient and cost-effective.
Beyond its role in batteries, nickel is also used in lightweight applications, such as high-strength steel alloys, combining durability with weight reduction. However, the growing demand for nickel raises concerns about its environmental and social impact, particularly in mining and processing. Responsible sourcing and recycling initiatives are essential to mitigating these effects. For example, recycling nickel from used batteries reduces the need for new mining, lowers production costs, and minimizes waste. The IEA predicts that widespread recycling initiatives could reduce the need for new lithium and nickel mining by approximately 25% by 2050, contributing to more sustainable supply chains.
Sustainable Materials Application In Automotive Manufacturing
Adopting circular economy practices transforms the automotive manufacturing landscape, focusing on minimizing waste and maximizing resource utilization. A circular economy approach involves designing vehicles and components with their entire lifecycle in mind, emphasizing modularity and ease of disassembly. This allows for efficient reuse, remanufacturing, and recycling of parts once the vehicle ends its service life. For instance, manufacturers are increasingly embracing the circular economy principles of reusing and reconditioning parts and fully recycling them only when their useful life is exhausted. Renault has embraced circular economy practices, including refurbishing EV batteries and reusing parts in its dedicated Re-Factory in Flins, France.
By integrating closed-loop systems, companies can ensure that materials extracted from end-of-life vehicles are processed and reintegrated into production lines. This approach conserves resources and reduces manufacturing costs and carbon emissions. As circular economy practices become more widespread, they highlight the need for collaboration across the supply chain and innovative design strategies to make vehicles more sustainable.
3D printing, or additive manufacturing, revolutionizes the automotive industry by enabling on-demand production and reducing material waste. Unlike traditional manufacturing methods, which often involve cutting away material to create components, additive manufacturing builds parts layer by layer, significantly minimizing excess material. This technology is particularly beneficial for producing lightweight and geometrically complex parts previously difficult or costly to manufacture. Automotive companies leverage 3D printing for various applications, including prototyping, tooling, and end-use components like customized interior trim or structural brackets.
Additionally, 3D printing allows manufacturers to localize production, reducing transportation costs and associated emissions. While scalability remains challenging, advancements in high-speed printing technologies and industrial-grade materials like aluminum alloys are gradually increasing the feasibility of large-scale production.
Improving energy efficiency in automotive manufacturing is essential for reducing the industry’s environmental impact and operational costs. Automakers are adopting various strategies to minimize energy consumption during production, such as optimizing processes, investing in energy-efficient machinery, and implementing advanced monitoring systems to reduce waste. To lower their carbon footprint, many manufacturing facilities are transitioning to renewable energy sources, such as solar, wind, and hydropower.
For example, Tesla’s Gigafactories aims to transition to 100% renewable energy, with significant reliance on solar installations and other green energy sources. Also, techniques like heat recovery systems and improved plant insulation help reduce energy losses. Companies are also exploring digital twin technologies to simulate and optimize energy use before implementing changes on the factory floor. By prioritizing energy efficiency, manufacturers enhance their sustainability credentials and achieve significant cost savings, proving eco-friendly practices are environmentally and economically beneficial.
Life Cycle Assessment (LCA) is a critical tool in the automotive industry, enabling manufacturers to evaluate the environmental impact of their vehicles across their entire lifecycle. This comprehensive approach considers every stage of a product’s journey, from raw material extraction and processing to manufacturing, use, and end-of-life disposal or recycling. By analyzing these stages, LCA helps identify the most resource-intensive and environmentally harmful processes, guiding manufacturers toward more sustainable alternatives.
For example, LCA can reveal that shifting from virgin materials to recycled inputs significantly reduces carbon emissions and energy use during production. Using recycled aluminum instead of virgin aluminum can reduce energy use by up to 95%.
Additionally, LCA is instrumental in assessing the long-term benefits of electric vehicles (EVs), accounting for factors like battery production and energy sources during the use phase. This data-driven methodology informs product design and material selection and supports compliance with regulatory frameworks and sustainability certifications. As the industry embraces sustainability, LCA provides the insights necessary to prioritize investments, innovate in green technologies, and achieve meaningful environmental improvements. It ultimately empowers manufacturers to make data-backed decisions that balance ecological responsibility with economic viability.
End-of-life vehicle (ELV) recycling has become a cornerstone of sustainability in the automotive industry, focusing on recovering valuable materials while reducing waste. When a vehicle reaches the end of its operational life, it undergoes a dismantling process where reusable components, such as engines, transmissions, and electronic modules, are salvaged for refurbishing or resale. The remaining structure is then processed to extract valuable materials like metals, plastics, and glass. For example, steel and aluminum from vehicle bodies are melted down and reused in manufacturing, while plastics are repurposed for components like bumpers and dashboards. This closed-loop approach minimizes the need for virgin material extraction and significantly reduces environmental impact. However, the complexity of modern vehicles, with their mix of materials and intricate designs, poses challenges for efficient dismantling and recycling. Innovations in automated sorting and advanced material separation technologies are critical to overcoming these obstacles, ensuring a higher recovery rate, and paving the way for more sustainable automotive production cycles.
With the rapid rise of electric vehicles (EVs), battery recycling has become a top priority in the automotive industry to address environmental and economic concerns. EV batteries, often made of materials like lithium, nickel, cobalt, and manganese, are resource-intensive to produce and potentially hazardous if not disposed of properly. Recycling these batteries enables the recovery of these critical materials, reducing the need for environmentally damaging mining operations.
Companies like Redwood Materials report up to 95% recovery efficiencies for valuable metals like cobalt and nickel, significantly contributing to resource conservation and waste reduction.
Beyond resource conservation, battery recycling mitigates the risk of pollution and supports the circular economy by integrating recovered materials into the supply chain. However, challenges such as the diversity of battery chemistries, lack of standardized recycling processes, and logistical hurdles in collecting end-of-life batteries need to be addressed. Governments and manufacturers increasingly invest in infrastructure and policies to ensure EV battery recycling becomes scalable and efficient, solidifying its role in a sustainable automotive ecosystem.
While the automotive industry is making significant moves toward sustainability, several challenges must be addressed to achieve widespread adoption of green practices.
One of the primary limitations is cost. Sustainable materials and advanced manufacturing technologies often have higher upfront expenses, making them less accessible for mass-market vehicles. Developing and implementing infrastructure to support circular economy practices, such as recycling facilities and supply chain logistics, requires substantial investment and cross-sector collaboration.
Technological barriers also persist, including the difficulty of recycling complex components like multi-material composites and the energy-intensive manufacturing of lightweight materials. Furthermore, regulatory inconsistencies across regions can hinder global progress, as manufacturers must navigate varying standards and policies.
Despite these challenges, the future of sustainability in the automotive sector is bright. Continuous advancements in material science, manufacturing techniques, and recycling technologies are driving down costs and improving efficiency. Collaborative efforts among automakers, governments, and technology providers pave the way for a more unified and effective approach to sustainability. As consumer demand for sustainable vehicles grows, automakers have a clear incentive to innovate and integrate these practices into their core operations.
The automotive industry stands at the forefront of the global shift toward sustainability, playing a crucial role in addressing some of our time’s most pressing environmental challenges. By adopting sustainable materials, innovative manufacturing techniques, and robust recycling practices, the sector demonstrates its ability to evolve and adapt to changing consumer expectations and regulatory demands. These efforts reduce the environmental impact of vehicles throughout their lifecycle and unlock new avenues for innovation and economic growth.
However, achieving true sustainability requires a collective commitment from all stakeholders, including manufacturers, suppliers, policymakers, and consumers. The automotive sector’s sustainability depends on continuous investment in material science, scalable recycling technologies, and collaboration across the supply chain. The industry can address environmental challenges by integrating these elements while driving innovation and competitiveness.
By embracing sustainability as a core value, the automotive sector can build a cleaner, more responsible world, inspiring other industries to follow suit.
Let’s talk.
How AI and ML enhance LiDAR technology by overcoming data processing challenges, enabling advanced applications in autonomous systems, robotics, and 3D mapping, and more.
Offering insights into how the latest AI advancements will impact consumers, manufacturers, and the broader environment in 2025 and beyond.
A comprehensive overview of Vehicle-to-Everything (V2X) communication technology, highlighting its role in creating a safer, smarter, and more connected transportation ecosystem.